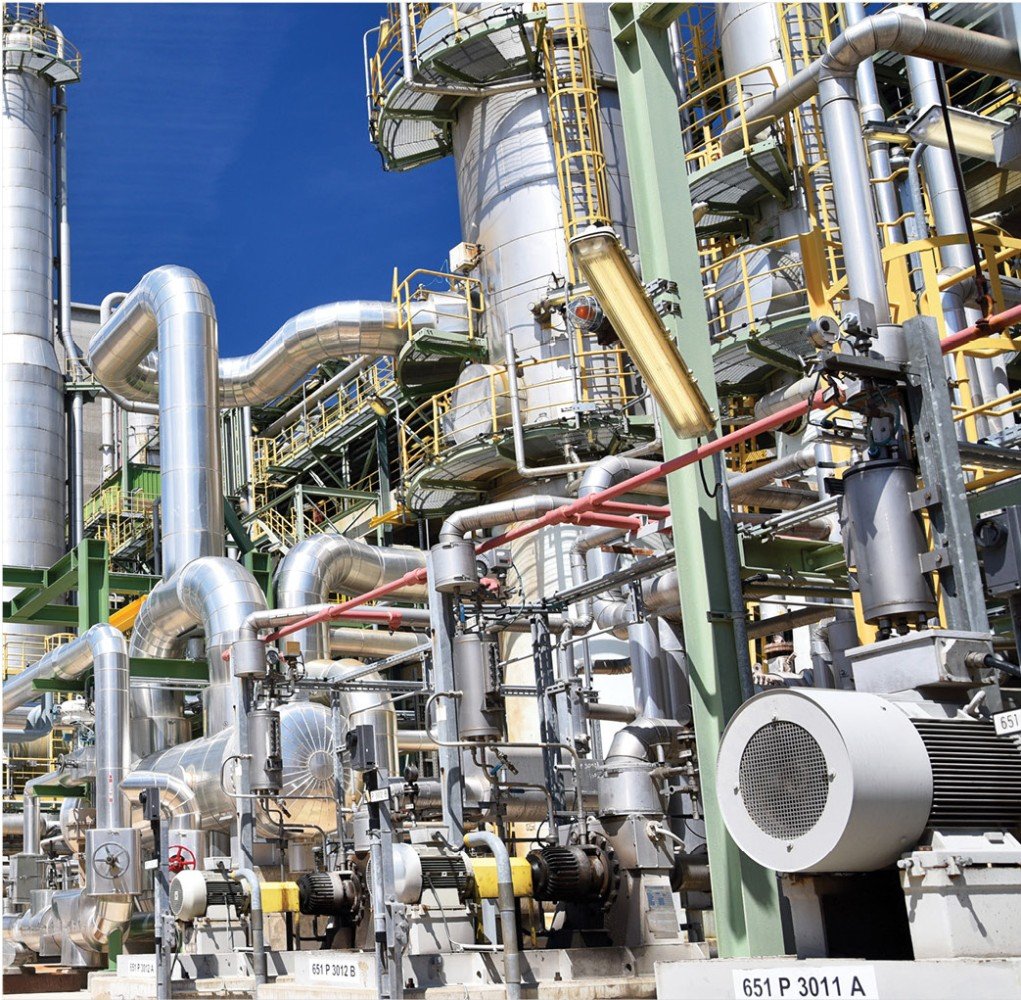
Effect on Heat Transfer
Effect on Heat Transfer
Coatings can little or negligible effect on heat transfer rates in heat exchangers. This effect heavily depends on the coating chemistry and thickness. However, this small decrease is often offset by the benefits they provide in preventing fouling and corrosion, which, if left unchecked, can severely impair heat transfer efficiency over time. Fouling, for example, causes deposits to form on heat exchanger surfaces, dramatically reducing thermal conductivity. Coatings can prevent these buildups by maintaining consistent heat transfer rates, ensuring the equipment operates at optimal efficiency. Coatings are often engineered to be thermally conductive, meaning they protect the exchanger without significantly impeding heat transfer. Ultimately, the right coating can improve the overall thermal performance of the system by reducing fouling-related losses and extending operational periods between maintenance.
The diagram below shows that uncoated bare tubes initially have a 100% heat transfer rate (HTR). Over time, as corrosion and fouling products accumulate, the HTR decreases until maintenance or cleaning is necessary. After cleaning, the HTR of the bare tube does not return to 100%, but to a lower value. With each subsequent maintenance or cleaning event, the HTR improves to a lesser extent than the previous cleaning. This process incurs maintenance and cleaning costs, as well as downtime for the plant.
In contrast, a coated tube starts with a slightly lower HTR than an uncoated bare tube. However, the coating is designed to prevent corrosion and fouling buildup, resulting in a more stable heat transfer rate over time.