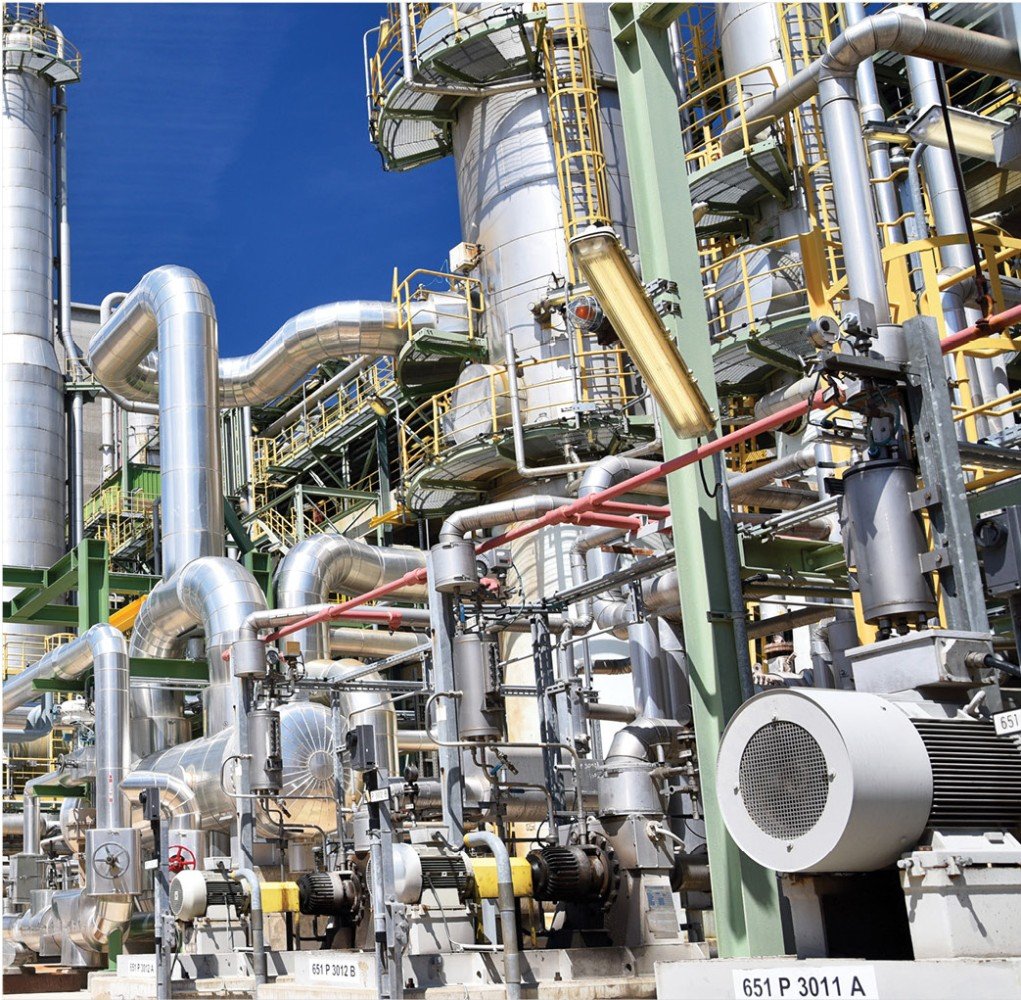
Application Process
Application Process
Applying coatings to the internal diameters (IDs) of heat exchanger tubes is a highly specialized process that ensures both quality and durability. The process begins with thorough surface preparation, which is critical to achieving proper adhesion. Typically, this involves abrasive blasting to White Metal Blast standards, such as SSPC-SP 5/NACE No. 1 or ISO 8501 Sa3, which removes any scale, rust, fouling, or contaminants from the tube walls. The internal surfaces must meet stringent cleanliness and roughness requirements, verified through borescope inspections and surface profile measurements to ensure optimal bonding of the coating.
Once the surface is prepared, the coating is applied using proprietary, state-of-the-art equipment that is both designed and manufactured in-house. This equipment is capable of performing both cleaning and coating of heat exchanger (HEX) tubes in a self-contained process. To guarantee accurate mixing, the coating components are blended using a static mixer. For each application, a detailed report is generated, outlining critical parameters. This data is automatically logged and sent via email to authorized recipients.
The equipment dispenses the exact amount of coating material based on the tube’s ID, length, and desired coating thickness, ensuring a uniform layer throughout. Achieving consistent coating thickness is crucial for meeting performance requirements, such as resistance to chemicals, abrasion, and thermal degradation.
After application, the coatings cure at ambient temperature. Post-application quality control (QA/QC) inspections are conducted, including dry film thickness (DFT) measurements and holiday testing, which helps detect any defects like pinholes or holidays.
When properly applied, these coatings not only enhance the performance of the heat exchanger but also reduce the need for maintenance, significantly extending the equipment’s service life.